Tooling and Materials – How to Choose a CNC Router Bit | 02.28.2024 | Techno CNC Systems Blog | 7 Minute Read
5 THINGS TO CONSIDER WHEN CHOOSING A CNC ROUTER BIT
Choosing the correct router bit is a process. There are many router bits designed for specific materials. Proper tool selection is imperative. We will go over materials below so you can better understand which router bits pair best with certain woods, plastics, foams, aluminums, etc.
- The first thing to consider when choosing a CNC router bit is the material you are cutting. What material, or materials, do you plan on using for your project? Each material requires a router bit with specific geometry so that it provides the best cut quality and performance.
- The second thing to consider is the size of your router bit. Typically, you want to try and use the largest tool possible because the larger the tool, the greater the rigidity of the tool, thus resulting in higher cut speeds. You also don’t want to use a tool that has too long of a length of cut. For example, if you want to cut ¼” thick material its best to use a cutter with 3/8” length of cut versus a 1” length of cut. The longer the tool, the weaker the tool. This will limit your speed and cut quality.
- The third thing to consider is the size of the part you plan on machining.
The larger the part the faster you can route, because the vacuum hold-down will better secure the raw material to the vacuum bed surface. For example: If you are routing a 2ft x 2ft board, you can use a large tool and route very fast because your vacuum hold-down on the machine will be able to secure this workpiece very effectively. With that being said, if you are routing a 4in x 4in piece, this is much harder to hold down because you have minimal surface area under the part to secure it to the vacuum table. For this scenario, you may want to use a smaller cutter because the cutting forces will be less, therefore applying less force to the workpiece.
TOOL MATERIALS
Solid Carbide
Solid Carbide are great to use for all natural woods, wood composites and hard, fibrous and abrasive plastics. Solid carbide is generally the toughest tool (next to diamond tooling) and holds the edge best.
Carbide Tipped
Use for plywood and coarse wood composites. Carbide tipped tooling provides some of the edge longevity of carbide with the lower cost of a steel base.
High-Speed Steel
Use for aluminum, soft natural woods and ABS or poly plastics. High-speed steel is the most readily available tooling and is preferred for most metal work because of its cost and hardness. HSS is seldom used in wood applications because carbide tooling stays sharper longer. HSS is generally prefered for metal cutting and some plastic cutting operations.
TOOL GEOMETRY
Straight Flute
Use for wood and plastic hand-free operations. The straight flute design, in single or multiple cutting edge, produces a clean finish. The harder the material, the more cutting edges are recommended.
Spiral Flute
Use for aluminum, wood and plastic machine-feed operations. The spiral flute is especially good at cleaning chips. When cutting aluminum and plastic, remelting of the chips is primarily the souce of poor cut quality.
Chipbreaker
Use for wood roughing or hogging machine-feed operations. The chipbreaker edges increase the overall cutting edge length allowing for much faster feed rates.
FLUTE GEOMETRY
Single Flute
Use for faster feed rates in softer materials. The single-flute cutter typically has lots of room for chips, but the single cutting edge limits either the feed rate or the hardness of the material to be cut. These type of cutters are especially recommended for plastics.
Double Flute
Use for better finish in harder materials. Double-flute bits provide a smoother cutting action because chip load is smaller than a single-flute cutter for a given feed. This allows harder materials to be handled.
Upcut Spiral
Use for grooving or slotting, for upward chip evacuation and best finish on bottom side of piece part. These bits allow for rapid cuts since the tool clears the chips away from the material. This type of tool is not recommended for softer materials such as MDF because of the ragged finish that can result on top of the surface.
Downcut Spiral
Use for downward chip flow, better holddown in fixture and best finish on top side of piece part. Note that the cutting speeds usually have to be reduced because the chips are purchased back into the material.
Up/down Spiral
Use for double-laminated material and best finish on top and bottom side of piece part. Because of the spirals, all the chips are forced back into the material. This results in a very clean cut on the top and bottom edges, but the cutting speeds have to be reduced. Note that the center of the spirals should be approximately in the center of the material for best results. This usually means that a substantial scavenger board would have to be used.
TECHNO CNC TOOLING
Techno CNC is proud to introduce our new CNC router bit product line. Techno CNC has developed tooling kits for specific routing market applications, making tooling selection for production shops easy.
Small Investment, Large Return
Efficient, affordable and budget-friendly CNC routers
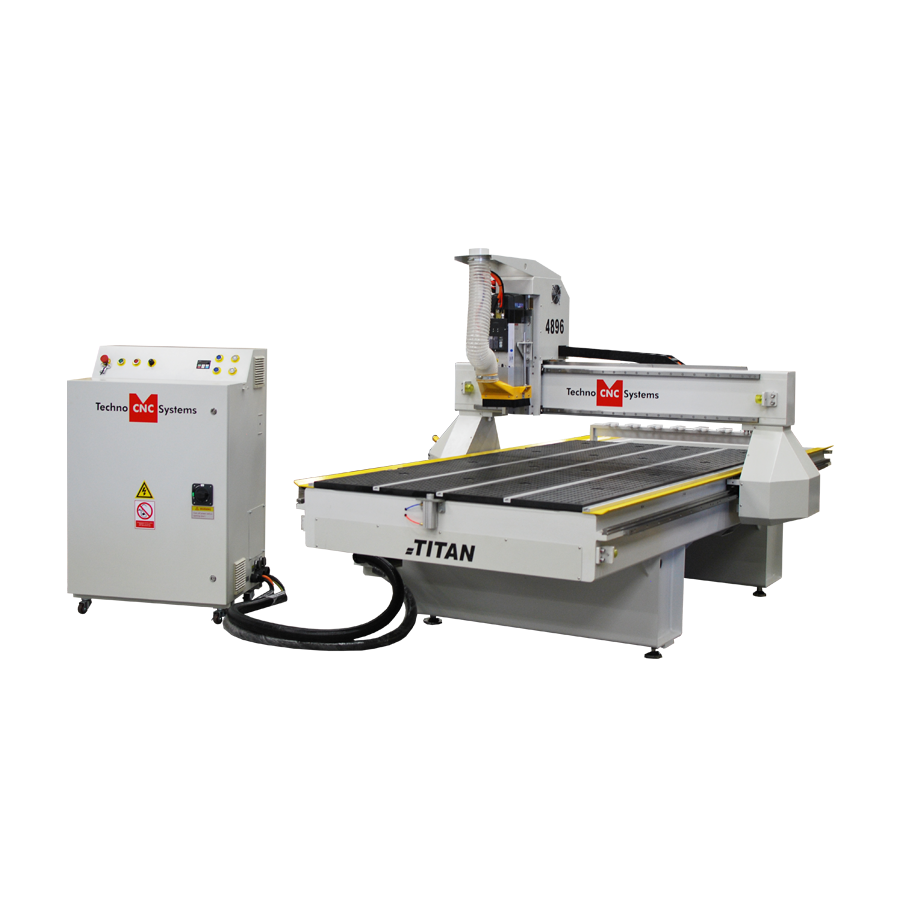
-
29 Trade Zone Drive
Ronkonkoma, NY 11779
- 631-648-7481
- technosales@technocnc.com